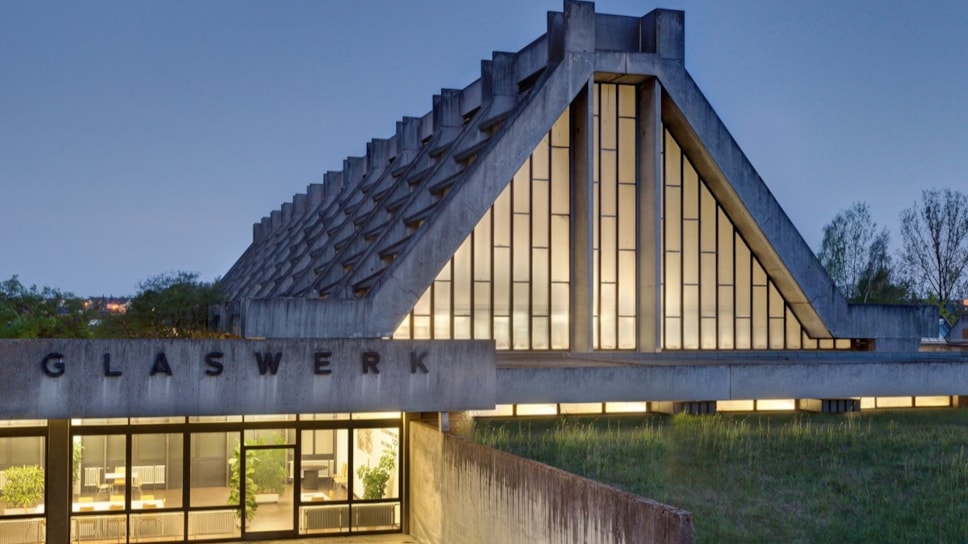
Making Modernism modern: when world-renowned architecture meets innovative technology
The iconic Bauhaus ‘Glass Cathedral’ factory – is to be equipped with state-of-the-art sustainability that converts waste heat into electricity, another example of energy being an asset that supports business.
- The listed ‘Glass Cathedral’ building in Amberg, Germany, dates back to 1970, and was one of the last projects by architect and Bauhaus founder Walter Gropius
- Owned by glass manufacturer Kristall-Glasfabrik Amberg, it makes about 23 million high-quality goblets and crystal glasses each year
- Glass production has a high energy demand – around 70 gigawatt hours is the same as the electricity demand of 25,000 average UK homes
- For the production process, the glass tank is continuously heated to a melting temperature of nearly 1,500 degrees
- Together E.ON and Orcan Energy work to deliver an innovative waste heat recovery system that optimises energy use and reduces CO₂ emissions
When world-renowned architecture meets innovative technology: In a groundbreaking initiative, E.ON and Orcan Energy have collaborated to bring a new energy efficiency system for the iconic 'Glass Cathedral' factory designed by renowned Bauhaus architect Walter Gropius.
This architectural gem, which dates back to 1970, is the production site for the Kristall-Glasfabrik Amberg glassworks.
With an annual output of approximately 23 million high-quality goblets and crystal glasses, the facility faces significant energy demands, requiring around 70 gigawatt hours. This innovative energy solution is driving sustainable industrial production and reducing CO2 emissions.
How does it work?The new energy system is called an Organic Rankine Cycle (ORC) which converts waste heat generated during the production process into electrical energy. By capturing waste heat from the manufacturing process and converting it into electrical energy, the ORC system offers a sustainable alternative to power the on-site operations without the need for additional fuel sources. This approach not only optimises energy consumption but also enhances the stability and efficiency of the manufacturing processes. |
Completed in 1970 – one year after Gropius’ death – the building came to be known as the ‘Glass Cathedral’ because of its 20-metre-high and 100-metre-long interior, designed to create a chimney effect above the glass furnaces, which produce a great deal of heat.
“The most challenging task of implementation was the planning process: the construction of the project had to be carried out within a six-week timeframe during the so-called 'tank revision'. Timing was of particular importance," says Christopher Link, project manager at E.ON.
This successful collaboration between E.ON and Orcan Energy highlights the potential in enhancing energy efficiency and in shaping a more environmentally conscious future for industrial processes. By effectively utilising waste heat, companies like Kristall-Glasfabrik Amberg can reduce their environmental impact while maximising their energy use.
This is just one of the ways E.ON is working to employ sustainable practices across industry by utilising waste heat. In the UK an agreement forged with Sheffield stainless steel manufacturer Marcegaglia will recover and distribute waste heat from the melting process into E.ON’s district heating network in the Lower Don Valley. Once operational, this will play a key role in enhancing the resilience of the region’s energy infrastructure and contribute to Sheffield City Council’s wider decarbonisation goals.