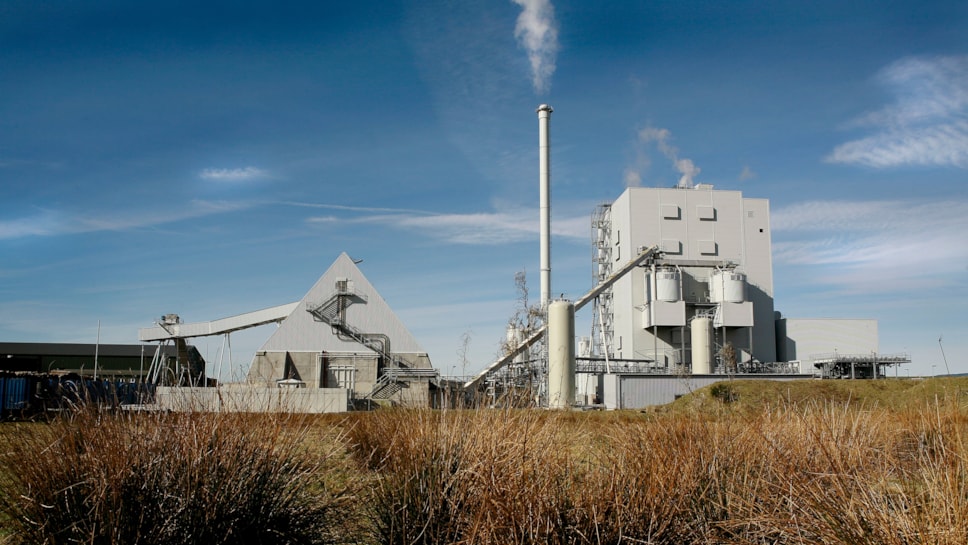
Made in Scotland: developing a sustainable fuel for ships, planes and racing cars
E.ON’s Steven’s Croft biomass plant joins Scotland’s HyLion network to establish a supply chain for hydrogen-based e-methanol – a sustainable fuel for global industries
Shipping, aviation and motorsport – all high octane (literally) sectors with the competing challenges of needing to source fuels for their operations while at the same time decarbonising their supply chains.
That’s where the HyLion alliance comes in – with E.ON’s Steven’s Croft biomass power station at its heart. Based in Scotland, partners in the HyLion alliance plan to develop a renewable energy source to create e-methanol, a more sustainable and alternative fuel to petrol and diesel.
This sustainable fuel can be used for a variety of applications, helping industries to transition away from fossil fuels and playing a significant role in reducing carbon footprints.
At the heart of this project is using renewable energy to create green hydrogen and what’s called ‘biogenic CO2’ – which is the carbon dioxide from organic material, from sources like the whisky production process and from biomass power plants.
How does the process work?
The first stage in the process is at the Steven’s Croft biomass power station, one of Scotland’s largest renewable energy plants, which uses waste wood from local timber, coppiced wood, and recycled fibres to generate electricity in a carbon-neutral way.
Opened in 2008, Steven’s Croft generates 44 megawatts of electricity – the equivalent power needs of 70,000 UK homes. By using biomass it saves about 140,000 tonnes of greenhouse gases every year compared to fossil fuel generation. That’s equivalent to taking tens of thousands of cars off the road.
Under the HyLion project, the biogenic CO2 that comes from Steven’s Croft and from the whisky production process will be captured, liquefied and stored.
In a separate process, we’ll also be generating green hydrogen at Steven’s Croft using an electrolyser – an apparatus that uses electricity to run a chemical process that separates the hydrogen and oxygen molecules from water.
The two ingredients in hand will then go through a process to combine them so they become e-methanol, a versatile fuel that can be utilised in a wide range of applications, from shipping to aviation to motorsport.
And it is a model that can offer a blueprint for other regions and other industries – all seeking to integrate renewable energy, secure CO2 supply, and take advantage of advanced digital monitoring – especially as future regulations are likely to support low-carbon fuels through stricter emissions standards.
The production of e-methanol is set to begin in 2028 with an initial capacity of 45,000 tonnes a year. But as the technology develops, and as the world’s appetite for green alternatives to fossil fuels grows, that number is expected to skyrocket.
Early forecasts suggest production could grow by up to ten times that initial pilot volume, which is especially important given the anticipated rise in demand for e-methanol as industries around the world work to reduce their carbon footprints.
:: HyLion partners include MHP Consulting (part of the Porsche group) as well as McPhy Energy, Bosch Manufacturing Solutions, CO2-Recovery Ltd & The Carbon Removers, Arup, Mareneco, Cadeler A/S and P1 Performance Fuels